Аби елеваторний бізнес у структурі агрохолдингу був прибутковим, треба зважено підходити до інвестицій і шукати оптимальні рішення.
Відвідати будь-який елеватор — означає дізнатись щось нове. І хоча технології зберігання зерна є сталими вже багато століть, на кожному підприємстві можна побачити особливості, що зменшують витрати, заощаджують ресурси, оптимізують роботу і дають змогу більше заробляти. Не став винятком і Зозівський елеватор, що входить до структури компанії «ТАС Агро».
Два в одному
Підприємство будували у два етапи — перший завершили ще 2004 року. Усе обладнання придбали в компанії ARAJ — сушарку, очисні машини й силоси на 10 тис. тонн одночасного зберігання. Враховуючи спеціалізацію, у конструкції силосів застосували гладкі металеві листи.
Другу чергу будували 2014 року з обладнання LORD, без підземних транспортних галерей. Розвантажують силоси за допомогою двох шнеків: один рухається всередині силоса й збирає зерно до центральної лійки, другий забирає зерно і подає його до ланцюгового транспортера. Таке рішення зменшило витрати на будівництво, але водночас додало незручностей — якщо шнек зупиняється, відвантаження припиняється. Також була й проблема пошкодження зерна, аж доки не почали використовувати полімерний захист шнеків.
Після будівництва другої черги потужності елеватора збільшились до 40 тис. тонн одночасного зберігання, але кожна черга, по суті, працювала окремо. Цьогоріч встановили один транспортер, який переміщує зерно з другої черги на першу, і на сьогодні очікується поставка другого транспортера від KMZ Industries, який дозволить переміщувати зерно у зворотному напрямку.
Двома групами силосів керують з одного робочого місця. Поки що працюють дві окремі системи керування в паралельному режимі, але після встановлення другого «об’єднуваного» транспортера системи керування планують також об’єднати в одну.
Незважаючи на те, що обладнання ARAJ розраховували під роботу із соняшником, воно може працювати з усіма іншими культурами. У другій черзі на лінії очищення встановлено накопичувальні бункери, які вміщують 40–50 т, що дає змогу тимчасово (до 1 год) вимикати транспортне обладнання для обслуговування або ремонту — процес очищення не припиняється.
Відкриваючи нові можливості
Підприємство приймає ячмінь, пшеницю, ріпак, сою, соняшник і кукурудзу. Залежно від урожайності оберти елеватора становлять 60–65 тис. тонн. За весь час підприємство жодного разу не робило менше як 1,5 оберту. Робота триває без зупинок, і після зачищення відразу приймають новий урожай. Наприклад, цього року від моменту відвантаження останнього торішнього зерна до завезення нового врожаю минуло усього два тижні. За цей час потрібно було виконати всі сервісні й ремонтні роботи, зачистити й обробити місткості й транспортні системи. Для цих робіт складають графік, якого намагаються чітко дотримуватись.
Закупати запчастини й ремкомплекти почали ще з Нового року, і навесні отримали все необхідне. Із середини квітня мірою звільнення силосів почали роботи з обслуговування й ремонту. До того ж елеватор функціонував у звичному режимі.
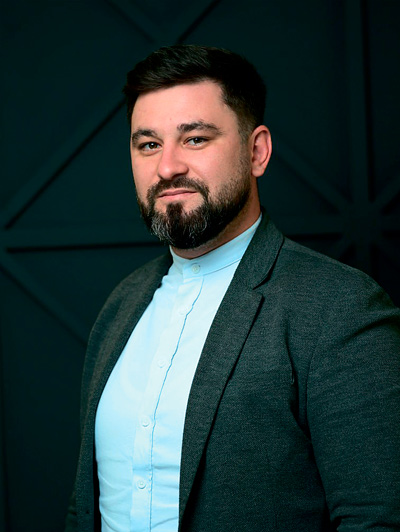
Для висотних робіт наймали підрядників, яким довелось постійно підлаштовуватись — зупинятись або працювати понаднормово. Це був певний виклик, оскільки минулий сезон був дуже напруженим. Хоча, за словами Ярослава Стратуци, директора елеваторного господарства «ТАС Агро», поточний сезон ще складніший. До цього року елеватори компанії завжди працювали з кожною культурою по черзі. Цього року через погодні умови довелось паралельно приймати по кілька культур. Ріпак, ячмінь і пшеницю збирали практично в один і той самий час, а одразу за ними в південному кластері дозріла кукурудза. Усі плани й графіки доводилось щодня корегувати, наймати додаткові комбайни й вантажний транспорт, оперативно переміщувати техніку. В умовах дефіциту кадрів зробити це було надзвичайно важко, але команда підприємства впоралась. Навіть ті працівники, що вже багато років працюють у компанії, дивувались, на що реально здатне їх підприємство. Доводилось встановлювати додаткові самопливи, запускати потоки зерна незвичними маршрутами… Однак усе це збільшило продуктивність приймання з 1000 т/добу до майже 2000, і це за одночасної роботи з двома або й трьома культурами! В осінній період розширили можливості з приймання кукурудзи — одночасно можуть приймати, очищати, сушити й відвантажувати.
Сушити економно
Зерно сушать у сушарках із твердопаливними теплогенераторами від ТОВ «Греко Груп». Вони працюють на соняшниковій пелеті. Переважну більшість сушарок оснащено двома теплогенераторами, оскільки основною культурою була кукурудза й надходила на елеватор із вологістю 20–24%. Відповідно, для сушіння такої кількості з необхідними можливостями сушарок вирішили встановлювати по два теплогенератори. Це забезпечує продуктивне сушіння з вологості 20–24 до 14–15% за температури теплоносія 120 °С. На сьогодні зняти 4% вологості пелетою коштує 60 грн, а з газом — 120 грн. І це при тому, що цьогоріч газ купували влітку, коли вартість була мінімальною. Тому твердопаливні котли окупились дуже швидко, за сезон-півтора.
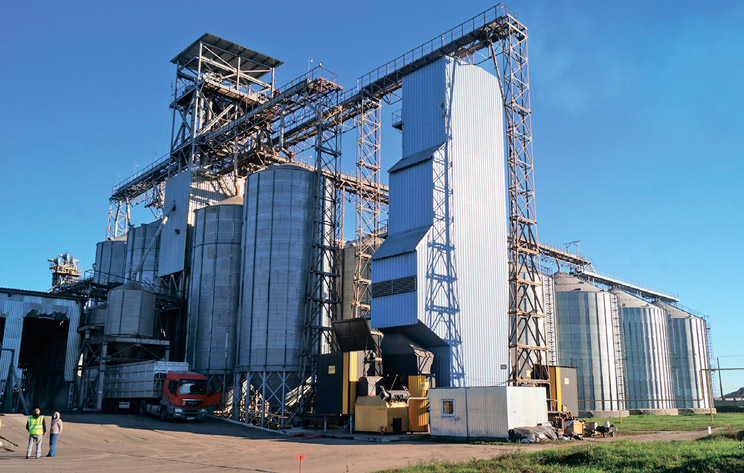
На Зозівському елеваторі встановлено дві сушарки — LORD і ARAJ. Перша працює з двома теплогенераторами, друга — з одним та ще й через теплообмінник. Так довелось зробити через технічні особливості сушарки ARAJ, яка не передбачена для роботи з теплогенератором. З іншого боку, певні культури можна сушити безпечніше. За ефективністю сушіння обидві сушарки видають паспортну продуктивність. Сушіння без теплообмінника не забруднює зерно. Кілька разів перевіряли, і жодного разу не було виходу за межі норм.
Гнучке зберігання
Коли порти були заблокованими, усім підприємствам компанії довелось оперативно вивчити технологію зберігання зерна в полімерних рукавах. Зозівський елеватор один із перших розпочав роботу у цьому напрямі — для цього придбали відповідне обладнання в компанії «Кобзаренко». Нині тут працюють із рукавами завдовжки 50, 60, 75 і навіть 90 м. Наприклад, пшеницю «пакують» у 75-метрові рукави через відносно невеликі строки зберігання. Це стосується як фуражної, так і продовольчої пшениці, і зберігають продовольче зерно на окремому майданчику, перед тим його очищають і охолоджують, а також піддають небулізації.
З кукурудзою працюють за трьома сценаріями. Для недовгого зберігання (1–2 місяці з вологістю зерна 19–21%) використовують 75-метрові або 90-метрові рукави. Так роблять, коли потрібно терміново завершити збирання до настання морозів, щоб уникнути зайвих пошкоджень і зберегти якість. Другий сценарій передбачає закладання кукурудзи з вологістю 15–18% на 2–3 місяці. Для тривалого зберігання (6 місяців і більше) кукурудзу сушать до 14–14,5% вологості, охолоджують і обробляють засобами захисту.
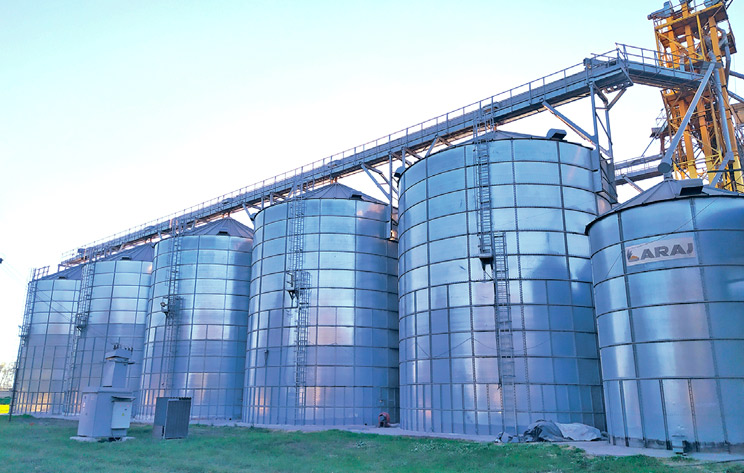
Для контролю стану зерна використовують кілька інструментів. Насамперед — це лабораторний контроль кожної вантажівки або перевантажувача. Це дає чітку картину, яке зерно й у якому місці рукава находиться. Температурні показники контролюють за тепловізорами. Дані з них передають через Wi-Fi на електронну базу, і лабораторія або оператор можуть відстежувати динаміку — силобег не пошкоджується, повітря не потрапляє всередину, не створюються умови для розвитку шкідників і хвороб. Така стратегія гарантує якість зберігання, і зерно можна після цього без проблем експортувати без ризиків щодо якості або зараження. Коефіцієнт втрат зерна в силобегах — 0,1%, що не перевищує природних втрат.
Майданчик для силобегів із двох боків захищають звуковими відлякувачами від птахів. Потім розкидають біопрепарати проти гризунів, щоб не наражати на ризик зернову продукцію. Проти лисиць і собак установлюють електропастухи.
Якість на рівні мистецтва
Як розповів Ярослав Стратуца, усі елеватори компанії забезпечили ручними експрес-аналізаторами для визначення вологості. Також придбали інфрачервоні автоматичні аналізатори для швидкого визначення якісних показників зерна, щоб зменшити час простою вантажівки до 15 хв. Окрім цього, розпочали оснащувати елеватори автоматичними пробовідбірниками з камерами й програмним визначенням точок відбору. Це значно скорочує час перебування вантажівок на території елеватора, пришвидшує приймання продукції.
Однак на цьому робота з якісними показниками не завершується. Окреме завдання — формування партій під контрактні вимоги. Через розбіжності контрактних вимог від ДСТУ доводиться формувати партії вже на етапі приймання та закладання на зберігання. І коли настає час везти зерно в порт, рідко трапляється, щоб партія повністю відповідала всім вимогам. Кожна партія зерна має свої показники якості, тому доводиться постійно аналізувати, чи вдасться відвантажити продукцію відповідно до вимог і чи буде технологічна можливість для отримання однорідної партії.
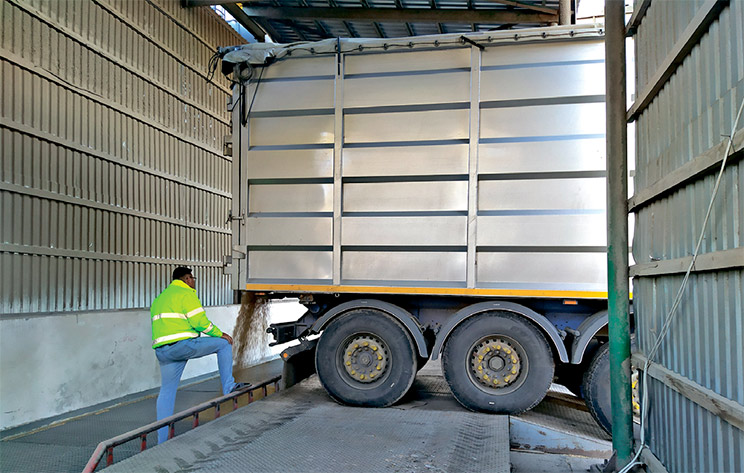
«Я починав кар’єру лаборантом і майстром, тож добре розумію, що кожен контракт вимагає творчого підходу до формування партії, — коментує Ярослав Стратуца. — Керівник лабораторії і старший майстер є основними фахівцями, які відповідають за цей процес. Завжди є зерно, яке за одним із показників не відповідає вимогам, і потрібно знайти рішення, яке дасть змогу змішати зерно, щоб воно відповідало вимогам. Щороку вимоги підвищуються, і так само щороку «вилазять» хвороби й шкідники, пошкодження зерна. Тому роботи з якісними показниками завжди вистачає.
Також багато часу забирають питання сертифікації. Наприклад, щоб отримати сертифікат «Дунайської сої», потрібно зробити експертизу і сертифікацію полів, ґрунтів, зеленої маси, процесу збирання, розміщення зерна на елеваторі, а також сертифікувати склади, де ця соя зберігатиметься. Сертифікат ISCC вимагає порахувати й підтвердити викиди СО2, що утворюється під час транспортування зерна з поля до елеватора і з елеватора в порт. Тому за контрактами до ЄС доводиться окрім якості враховувати й логістичну складову, оскільки з певних елеваторів зерно потрібно возити тільки залізницею».
Покращити й удосконалити
Ярослав Стратуца поділився власним баченням того, яким має бути ефективний елеватор. Він зазначив, що в технічному плані треба використовувати всі наявні рішення, які сприяють економії і зменшенню втрат. Однак водночас немає потреби переплачувати за бренди, якщо вітчизняні виробники можуть запропонувати хорошу та якісну альтернативу. Тож щодо обладнання, то ситуація проста — усе залежить від наявності грошей і готовності інвестувати.
Значно важливішим питанням є кадровий «голод». На сьогодні в Україні тільки кілька навчальних закладів готують спеціалістів зі зберігання зерна, та ті не хочуть працювати за фахом через низьку популярність професії. Навіть незважаючи на цікаві умови, знайти лаборанта або майстра дуже важко.
Ще один важливий аспект — це техніка для визначення якості продукції. Потрібно приймати зерно якомога швидше, і для цього доводиться купувати найсучасніші прилади й максимально автоматизувати процес визначення якісних показників зерна.
Від компонування та інфраструктури елеватора також залежить його ефективність. Наприклад, відбір проб і зважування мають відбуватись на одному місці, без додаткових переїздів вантажівки. Рух територією також має бути мінімізований.
«На мою думку через п’ять років Україна прийде до європейської системи зберігання зерна, — каже Ярослав Стратуца. — Великі елеватори на 100 тис. тонн більше не будуватимуть. Їх час минув. Якщо на малому елеваторі стоятиме достатньо технологічного обладнання і він буде гнучким, здатним працювати з усіма культурами й одночасно виконувати будь-які завдання, це забезпечить нечувану продуктивність за мінімальних інвестицій.
На сьогодні наша компанія розглядає питання збільшення елеваторних потужностей, але нас не цікавлять 100-тисячники. Краще маленький елеватор на 40–50 тис. тонн, і збоку — поле під силобеги, ніж великий елеватор із великим штатом працівників. Ми маємо досвід роботи нашого Талалаївського елеватора, який має складів на 55 тис. тонн і перевалює за сезон 220 тис. тонн. Такий підхід дозволяє швидко повертати інвестиції й отримувати прибуток».
Матеріал на agrotimes.ua